今回は、個別原価計算と総合原価計算についてお話します。
個別のモノの原価を把握する「個別原価計算」
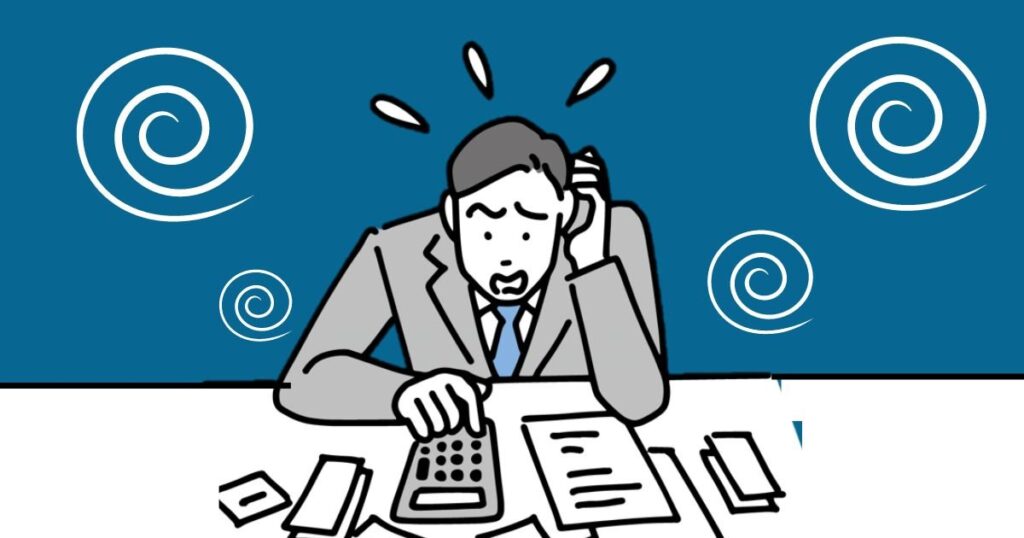
個別原価計算とは
個別原価計算とは、個別の製品ごとに原価を計算する手法です。個別受注生産の原価計算によく使われます。個別受注生産とは、一品一品違うもの、たとえば特注の機械や特注の建設資材部品などを、受注してから個別に仕様を決めて生産する製造形態です。
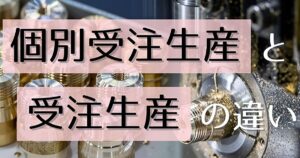
原価の教科書などには、個別原価計算は「製造指図№ごとに原価を集計する」と書かれていることが多いようですが、実際には、「製造指図№」の代わりに、「受注番号」や「製造番号」を別に集計する例をよく見かけます。
まず、直接材料費・直接労務費・直接経費を、受注番号や製造番号、要は個別の受注ごとに集計します。一方、間接材料費・間接労務費・間接経費も、それぞれ適切な基準で各受注に配賦する必要があります。正確な原価計算をするためには、製造に関する実績のデータを正確にとり、きちんとした基準で製品ごとに費用を振り分ける必要があります。
直接費用の把握
まずは直接費用についてみていきましょう。直接材料費を正しく把握するには、受注ごとに使用した材料の量を正確に記録することが重要です。
材料を手配する際、一般的には、ある受注のために使用することが決まっている原材料は、製造番号などで受注と紐付けをしてから購入します。ですが、最低発注量など、仕入先との間に制約条件がある関係で、必要以上の量を発注する場合もあります。その場合、必ずしも購入量がそのまま使用量と一致するわけではないので、買った量ではなく、実際に使った量を正確に測って記録する必要があります。
直接労務費も同じように、どの受注の作業を、どれだけの時間で行ったかを正確に記録しなければ、正しい把握ができません。
例えば、ある作業者が1日中、1つの受注に紐づく作業だけを行っていたのであれば、時間を記録することは簡単です。しかし、1人で複数の受注に関する作業を行う場合は、作業を行うたびに細かく時間を記録しておかないといけません。1日が終わってから正確な時間をまとめて思い出して記録するのは困難です。
直接経費はどうでしょうか。外注費については、複数の受注がある場合に、それぞれの受注ごとに作業を発注しているのであれば大丈夫です。しかし、事務手続きを省力化するために、まとめて発注することもありますよね。このようなパターンも、きちんと受注ごとの金額で費用計上できているかが重要です。もし計上できていなければ、間接経費のように配賦するしかなくなります。
間接費用の配賦
では次に、その間接費の配賦を見てみましょう。原価を正確に計算するためには、間接費を可能な限り生産活動にそった基準で配賦することがとても重要です。これを実現するためには、配賦基準の設定が鍵となります。一般的に、間接費の配賦方法には、部門別配賦と製品別配賦があります。個別原価計算なら、個別の製品別に間接費を配賦します。
では、1つ1つの製品に間接費を配賦するとして、その割り振りの基準はどのように定めたらいいのでしょうか。人数比、売上高比、作業時間比……。
活動基準原価計算、ABC(アクティビティベースドコスティング)という考え方があります。これは、できるだけ生産活動の実態にそってコストを計算するという考え方です。そのために、製品を生産するための活動=アクティビティを基準に配賦をします。一見当たり前のようですが、実は配賦の基準によっては、間接費の配賦結果と、その製品を作るために実際にかかった費用とが大きく乖離することがあります。そのことに対する問題意識から生まれたのが、ABCの考え方です。
「総合原価計算」とは
個別原価計算とは異なる原価計算の手法に、「総合原価計算」があります。個別原価計算では製品ごとに原価を集計しますが、総合原価計算では、一定の期間(たいていはひと月ごと)の間に発生した原価をまとめて、この期間に完成した製品の原価として計算します。一般的に、同じような製品を反復して大量生産する場合に適用されます。
同じ製品を反復して大量生産する場合に行うのは、最も単純な総合原価計算です。一方、同じ性質を持つが形がちがう製品、例えばサイズ違いなどのモノをいろいろと作る場合には、「等級別総合原価計算」というものを行い、違う性質を持つ異なる製品、例えば、椅子と机を同じ工程で製造する場合には、「組別総合原価計算」を行います。また、原価を計算する単位を製造品目よりもっと詳細にしたい場合は、同じ品目のロット別で原価計算をすることもあります。
デカップリングポイントと原価計算手法
デカップリングポイントとは、生産管理における見込生産と受注生産の分岐点です。見込生産は需要を予測し、受注より前にモノを作ります。受注生産は、受注してからモノを作りはじめます。
実際の製造業は、完全に予測して作る場合と完全に受注してから作る場合の間に、さまざまなデカップリングポイント=このタイミングで受注を受けるという分岐点があります。そのポイントによって、適している原価計算の手法が変わります。
MTS(Make To Stock)見込み生産
需要を予測して見込みで生産し、製品在庫を持つ生産方法です。同質なモノをまとめて作るので、総合原価計算を使います。
ATO(Assemble to Order) 受注組立生産
BTO(Build to Order)とも呼ばれます。同じ性質の中間品までを見込みで生産して、在庫として保有し、受注が入ると、中間品を注文に合わせて組み立てて出荷します。中間品までは同じで、そこから先の組み立てでカスタマイズするイメージです。中間品までのところで一度総合原価計算をして単位原価を求め、中間品を使った製品は別途個別原価計算を行います。ちなみに、中間品の見込み生産は一般的にロット単位で行うので、先ほど挙げたような同品目ロット別の総合原価計算をしたりもします。
MTO(Make to Order) 繰返しの受注生産
あらかじめ設計や仕様は決まっており、受注が入ったら、原材料の調達・製造をする方式です。受注後に原材料の調達から行う場合は個別原価計算をしますが、実際には、繰り返し生産のペースが速く、納期や調達、生産のリードタイムが合わないために、見込みで調達したり中間品までを生産したりする場合もあります。その場合には、ATO(受注組立生産)に近い管理になります。
ETO(Engineering to Order) 個別受注生産
このコラムの冒頭で、個別原価計算の主な対象として挙げた生産方式です。受注が入ってから設計や仕様決定をして、調達から製造はそのあとに行う、純粋な「受注生産」です。
製造業向けクラウド生産管理システムUM SaaS Cloud
個別原価計算と総合原価計算について、基本をご理解いただけたでしょうか。
シナプスイノベーションが提供するクラウド生産管理システムUM SaaS Cloudは、生産管理から販売・購買管理、在庫管理まで幅広く対応できる製造業向けシステムです。
原価計算に対応できるオプション製品「UM原価」もご用意していますので、ご興味のある方はぜひ当社製品ページをご覧ください。